Electricity supply requires some specific machines, where switchgear is one of them. It is a set of components that contribute to a stable supply of current without posing any electric threat. Industrial, commercial, and domestic sectors heavily rely on the transformation of electricity from high to low, low to medium, and vice versa. What are these switchgears, and how do they perform? You will find all the information you need in this switchgear preventive maintenance guide. What is an Electrical Switchgear? It is an umbrella term used to describe a set of devices that transform voltage, protect against surges and short circuits, and help regulate the flow of current from a considerable input to a small one and vice versa. They contain various components that conduct incoming electricity either from the grid or a higher transformer to appliances or substations. Here is a guide that can help you understand it in simpler terms. Why Does Preventive Maintenance Matter? Every machine requires regular maintenance to function optimally and prevent future failures. Likewise, electrical switchgear also requires preventive maintenance to operate efficiently. Not doing it will lead to power failure, short circuit, or reduced efficiency in the process. Things can get worse if the fire breaks out in the worst-case scenario. Predictive, Preventive, and Corrective Maintenance Types Here are three types of maintenance commonly followed in the industry. These three types are predictive, preventive, and corrective. If we describe them in simple terms, here they are. 1. Predictive This maintenance takes place when there is no problem at all. However, the purpose of this maintenance is to prevent any future issues. It facilitates basic checks and tests by monitoring and collecting data through sensing devices. Predictive maintenance helps to identify potential failures in switchgear, and its maintenance costs are high. However, the overall risk of an accident is the lowest compared to other types. 2. Preventive This maintenance takes place periodically, much like general maintenance. Preventing maintenance includes regular inspection and maintenance on a monthly, semi-annual, and annual basis. It consists of a physical inspection of components. Its cost is less than the above one, and safety is also less than that, but it is more reliable than the corrective. 3. Corrective Then, the third maintenance type occurs when something has already happened, such as failure, damage, or a minor malfunction. Corrective maintenance is performed after the failure occurs, which makes it riskier and more costly than the other types. What are the Recommended Maintenance Schedules in It? There should be different inspection and maintenance schedules for the various components in the electrical switchgear. Some require frequent inspections, while others require inspections after a specific period has passed. ✅ Perform daily or weekly checks, which are usually based on visual inspections. ✅ Then, some inspections are based on monthly or quarterly periods, focusing on the safety and installation of the components. It includes torque checks, which cover all types of tool tightening operations to mitigate the risks of accidents. ✅ Some tests are physical, while others are non-physical. Thermography is also a part of the maintenance schedule, which is performed through an infrared device to detect flaws in switchgear. ✅ There are over ten types of tests, and the insulation resistance test is one of them. It is performed to identify insulation degradation, which could result in insulation failure, moisture, and contamination inside the switchgear. Visual Inspection Checklist Visual inspection clears up lots of doubts regarding the apparent flaws in the switchgear. It could be about loose connections, corrosion, discoloration, or worn gaskets. Maintenance experts must inspect all components for potential replacement and repair. It includes cleansing of dust particles and moisture layers. What to Look for in Each Component Since lots of components are in a switchgear, each requires specific attention. Some require replacement of springs to function correctly, while others necessitate removal of the corrosion layer to operate properly. Circuit breakers, isolators, fuses, terminals, relays, busbars, insulators, and all these components require physical inspection to work well. Electrical Connection Testing Again, numerous tests are conducted in the industry to ensure switchgears operate optimally. If we point out some, here they are. • Thermographic inspection enables engineers to detect loose connections and areas of heat dissipation through hot-spot detection. This test is performed using a thermal detection device, making it a non-destructive method. • Then there is contact resistance measurement, which is also known as a micro-ohmmeter test. It allows engineers to inspect increased resistance, which could lead to failure later. Poor connection or oxidation are some possible reasons that can be detected through this test. • Another test is performed, which is torque verification. It is a physical inspection where engineers secure every component with tools to match the manufacturer’s specifications. How to do Its Cleaning and Insulation? The cleaning process is very risky since it is an electric system, which is highly hazardous to human and animal lives. A proven method is followed to perform cleaning and insulation of switchgear. The purpose is to prevent moisture ingress in the switchgear, as it can damage its internal system. • What engineers do is wear a PPE suit that meets the electric industry’s safety requirements • Additionally, they ensure that only non-metallic cleaning tools are used during the process. • They deenergize the switchgear and follow the Lock Out/Tag Out process before starting the cleaning process. • It includes various methods for cleaning the components, as some require dry methods while others require wet cleaning. • Once they have cleaned, they dry the components properly after using any cleaning solvent. Lubrication of Moving Parts Maintenance includes lubricating moving parts to reduce friction and prevent corrosion. It is a global procedure for almost every type of moving part in any machinery. Circuit breakers, switches, and various components require lubrication to function efficiently. Not doing that will cause jamming and poor response from the switchgears. Advanced Diagnostic Testing Additionally, there are advanced diagnostic testing methods, which include the use of infrared thermography. It helps in highlighting the faulty components that need attention. Thermal detection reveals areas of heat dissipation, indicating where to replace or repair defective components. Another test is then performed, which involves partial discharge monitoring. It helps detect the tiny discharges that occur in high-voltage insulated equipment. It works against massive outages later by curbing them in the beginning. Perform Environmental and Condition Monitoring Environmental threats can’t be overlooked because they pose numerous challenges for switchgears. Therefore, continuous monitoring is performed to detect changes in temperature, humidity, and ventilation inside and around the switchgears. Then, data collection and analysis are done to manage the components inside the switchgears. It helps against the risk of overheating, sparking, and moisture-related outages in the switchgears. Usage of Tools, PPE, and Safety Procedures Unless engineers use the correct tools and safety equipment, they are not permitted to approach the switchgear. It is strictly followed for the safety of engineers and also the switchgear systems. Therefore, they must perform Lockout/Tagout (LOTO) steps to ensure that no human error can occur related to reenergizing the switchgear during maintenance. They deenergize the whole system by applying tags and locks. Then, they must wear a PPE suit, which includes rubber gloves, rubber shoes, and a safety helmet. Additionally, arc-flash suits are worn during the maintenance process to protect against the risk of injury. How to Prevent Common Failures in Electrical Switchgear? The best way to prevent common failures is to perform timely maintenance. Regular inspection will keep you updated with components. Any potential risk, such as overheating and loose connections, can be detected through regular inspections. Mechanical wear in moving parts will never go unchecked when a specific maintenance time is specified. Timely inspection and replacement of parts must not be skipped. Keep the Records and Reports Then, the last thing is record-keeping, which facilitates in-depth analysis. When the maintenance records are available, it will be easier to detect the flaws. Historical data helps pinpoint the problem. Your analysis team will share the precise details regarding the flaw and its solution. This is why data collection, monitoring, and analysis are a must. Conclusion Operating electrical switchgear and keeping it maintained is not an easy task. It requires rigorous efforts to keep the system intact. Any mistake could lead to unbearable consequences. Therefore, industries maintain strict maintenance schedules to minimize the risk of accidents. Commonly Asked Questions 1. How often should you maintain electrical switchgear? From regular to annual methods, you have to perform the inspection accordingly. Some parts require frequent inspection, while others necessitate monthly or yearly inspections. 2. What are the key points in the electrical switchgear maintenance checklist? Visual inspections, physical and non-physical tests, component cleansing and lubrication, PPE suits, and safety LOTO methods are some key points to consider. Keep the documentation regarding every inspection along with historical data. Ensure that all grounding methods are followed before maintenance begins. 3. Can I perform preventive maintenance on the switchgear while it is energized? It is dangerous to perform this task when the switchgear is energized. Only thermal inspection is performed to detect heat dissipation on faulty parts. Otherwise, all maintenance is performed after the system is deenergized. 4. Are switchgear and switchboard the Same? No, Switchgear handles high-voltage power (up to 350 kV) and includes safety features like automatic shut-offs. It’s used for protection and control. Switchboards manage lower voltages (under 600V) and mainly distribute electricity. If you're running complex or large systems, go with switchgear.
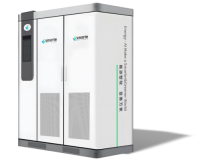
372 kWh Industrial and Commercial Liquid-Cooled Outdoor Cabinets